From Concept to Creation: Exploring the Role of 3D Modeling in Product Design and Prototyping
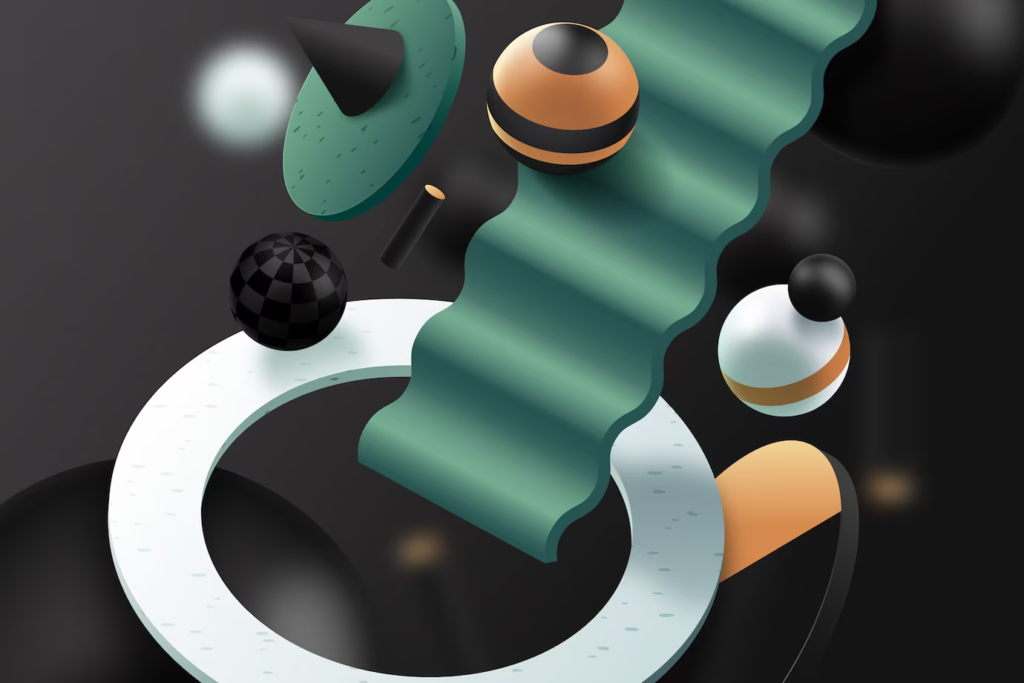
In the realm of product design and development, 3D modeling has become an indispensable tool, facilitating the transition from initial concept to final creation. This article delves into the multifaceted role of 3D modeling in product design and prototyping, exploring its applications, advantages, challenges, and future trends.
Introduction:
The journey from conceptualizing a product idea to bringing it to fruition involves numerous stages of design, iteration, and prototyping. In recent years, 3D modeling has emerged as a cornerstone technology in this process, enabling designers and engineers to visualize, refine, and validate their ideas with unprecedented precision and efficiency. This article examines the pivotal role played by 3D modeling in product design and prototyping, shedding light on its transformative impact on innovation and creativity.
Applications of 3D Modeling in Product Design
Conceptualization and Ideation: 3D modeling software provides designers with a versatile platform to explore and refine their product concepts in a virtual environment. By translating abstract ideas into tangible visual representations, designers can iterate rapidly, experiment with different design variations, and solicit feedback from stakeholders.
Visualization and Communication: Communicating design intent is crucial in the product development process, especially when collaborating with interdisciplinary teams or presenting concepts to clients. 3D models serve as powerful communication tools, enabling stakeholders to visualize and interact with product designs from multiple perspectives, fostering clearer understanding and alignment.
Iterative Design and Optimization: The iterative nature of product design demands continuous refinement and optimization to meet performance requirements and user preferences. 3D modeling facilitates rapid prototyping and design iteration, allowing designers to evaluate different design iterations, identify potential issues, and make informed decisions early in the development cycle.
Simulation and Analysis: 3D modeling software integrates simulation and analysis tools that enable designers to assess the structural integrity, functionality, and performance of their designs virtually. By simulating real-world conditions and conducting virtual tests, designers can anticipate and address potential issues before physical prototyping, saving time and resources.
Advantages of 3D Modeling in Product Prototyping
Cost Savings: Traditional prototyping methods, such as machining or molding, can be time-consuming and costly, especially for complex geometries or low-volume production runs. 3D printing, enabled by 3D modeling, offers a cost-effective alternative for rapid prototyping, allowing designers to iterate quickly and inexpensively without the need for specialized tooling.
Time Efficiency: Conventional prototyping processes often involve lengthy lead times, from designing tooling to producing physical prototypes. 3D modeling accelerates the prototyping process by eliminating the need for manual craftsmanship and enabling rapid iteration through digital design files, reducing time-to-market and enhancing agility in product development.
Customization and Personalization: Consumer preferences are increasingly gravitating towards personalized products tailored to individual needs and preferences. 3D modeling enables designers to create customizable product designs, accommodating variations in size, shape, or functionality to cater to diverse customer demands effectively.
Risk Mitigation: Prototyping serves as a crucial stage in identifying and mitigating potential design flaws or performance issues before mass production. By leveraging 3D modeling for virtual prototyping, designers can simulate and evaluate design alternatives, validate product performance, and minimize the risk of costly errors or product recalls down the line.
Challenges and Considerations in 3D Modeling for Product Design
Skill and Expertise: Mastering 3D modeling software requires proficiency in technical skills and design principles, posing a learning curve for designers transitioning from traditional 2D drafting methods. Continuous training and skill development are essential to harness the full potential of 3D modeling tools and techniques effectively.
Integration with CAD/CAM Systems: Seamless integration between 3D modeling software and computer-aided design/computer-aided manufacturing (CAD/CAM) systems is critical for maintaining design fidelity and ensuring compatibility with manufacturing processes. Designers must navigate interoperability challenges and optimize workflows to streamline data exchange between different software platforms.
Material Selection and Compatibility: Material properties play a vital role in determining the performance, aesthetics, and manufacturability of prototypes. Designers must consider material properties, such as strength, flexibility, and thermal conductivity, and ensure compatibility with chosen prototyping methods, whether additive manufacturing (e.g., 3D printing) or subtractive manufacturing (e.g., CNC machining).
Cost-Benefit Analysis: While 3D modeling and prototyping offer numerous benefits, designers must conduct cost-benefit analyses to evaluate the economic viability of different prototyping methods. Factors such as material costs, equipment investment, and production volume influence the overall cost-effectiveness of prototyping solutions and inform decision-making processes.
Future Trends in 3D Modeling for Product Design and Prototyping
Advancements in Additive Manufacturing: The evolution of additive manufacturing technologies, including faster printing speeds, expanded material options, and improved resolution, will further democratize prototyping and enable the production of highly complex geometries with enhanced precision and efficiency.
Integration of AI and Generative Design: AI-driven design tools and generative design algorithms hold promise for automating design exploration and optimization, generating innovative solutions based on user-defined constraints and performance criteria. By leveraging machine learning algorithms, designers can explore a broader design space and uncover novel solutions that may not be apparent through traditional design methods.
Cloud-Based Collaboration and Simulation: Cloud-based platforms offer collaborative environments for distributed teams to collaborate on design projects seamlessly. Integrating simulation and analysis capabilities within cloud-based platforms enables designers to conduct virtual tests, iterate designs, and validate performance across diverse computing environments, enhancing collaboration and workflow efficiency.
Sustainable Design and Materials Innovation: As sustainability becomes a paramount concern in product design and manufacturing, designers are increasingly prioritizing environmentally friendly materials and sustainable manufacturing processes. 3D modeling facilitates the exploration of sustainable design alternatives, allowing designers to optimize material usage, minimize waste, and reduce the environmental footprint of products throughout their lifecycle.
Conclusion
In conclusion, 3D modeling plays a pivotal role in every stage of the product design and development process, from conceptualization and visualization to prototyping and production. By leveraging the power of digital modeling tools, designers can innovate, iterate, and optimize product designs with unprecedented precision, efficiency, and agility. While challenges such as skill acquisition, integration complexities, and material selection persist, ongoing advancements in technology and evolving industry trends promise to redefine the future of product design and prototyping, driving innovation and sustainability in a rapidly evolving marketplace.